Valves play a crucial role in controlling the flow of fluids and gases within various industries and applications. They are mechanical devices that enable start, stop, or regulation of flow, providing efficient control and optimization of systems.
A valve typically consists of components such as a body, seat, and closure element, which work together to control the flow. The body forms the main structure, providing a conduit for the fluid or gas. The seat acts as a sealing surface, ensuring a tight closure when the valve is closed. The closure element, such as a disc, gate, or ball, controls the flow by opening, closing, or partially obstructing the passage.
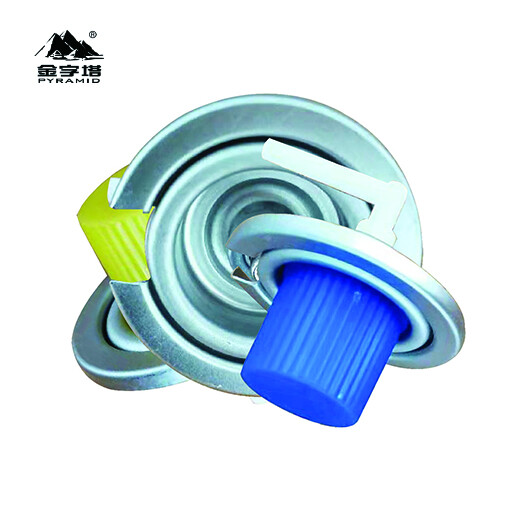
Valve Detail Introduction
A valve is a mechanical device that controls the flow of fluids or gases by opening, closing, or partially obstructing the passage within a system. Valves are essential components in various industries, enabling the regulation of flow rates, pressures, and the isolation of equipment when necessary.
Valves consist of several key components, including the body, seat, and disc. The body forms the main structure of the valve and provides the conduit for the fluid or gas. The seat acts as a sealing surface, ensuring a tight closure when the valve is closed. The disc, also known as the closure element, is responsible for controlling the flow by opening or closing the passage.
There are various types of valves designed to meet different application requirements. Some common valve types include gate valves, ball valves, globe valves, check valves, and control valves. Each type has its unique features, mechanisms, and specific uses.
1.What is a Valve?
A valve is a mechanical device that plays a critical role in controlling the flow of fluids or gases within a system. Its primary function is to start, stop, or regulate the flow, enabling efficient operation and control over the fluid or gas medium.
Valves operate by utilizing different mechanisms to control the flow. When open, valves allow the fluid or gas to pass through, enabling unrestricted flow. When closed, valves block the passage, preventing the flow altogether. Some valves offer the ability to regulate the flow by partially opening or closing the passage to achieve the desired flow rate.
Different types of valves are designed to cater to specific applications. For instance, gate valves are commonly used in applications that require full flow or shut-off, while ball valves offer quick and reliable control with minimal pressure drop. Globe valves are suitable for regulating flow, and check valves allow one-way flow while preventing backflow.
2. How Does a Valve Work?
Valves work based on fundamental principles of fluid dynamics and mechanical engineering. The working principle of a valve involves the movement of its internal components to control the flow of fluids or gases.
The key components of a valve include the body, seat, and disc. The body serves as the main structure, housing the other components and providing the passage for the fluid or gas. The seat acts as a sealing surface, ensuring a tight closure when the valve is in the closed position. The disc, which is connected to a stem or spindle, controls the flow by moving in response to the operating mechanism.
Different types of valves employ various mechanisms to regulate the flow. For example, gate valves use a gate or wedge-shaped disc that moves perpendicular to the flow direction to open or close the passage fully. Ball valves, on the other hand, use a rotating ball with a bore to control the flow. Butterfly valves use a disc that rotates on a shaft to regulate the flow by changing the degree of obstruction.
Understanding the working principle and mechanisms of different types of valves is crucial for selecting the appropriate valve for a specific application and ensuring efficient flow control.
3. Importance of Valves in Industries
Valves play a vital role in a wide range of industries, where precise control of flow, pressure, and isolation is crucial. Here are some examples of how valves are indispensable in various industries:
Oil and Gas Industry: Valves are used extensively in oil and gas production, refining, and distribution processes. They control the flow of oil, gas, and other fluids within pipelines, storage tanks, and processing facilities. Valves ensure safe and efficient operation by regulating pressure, directing the flow to different destinations, and isolating equipment for maintenance or emergencies.
Water Treatment: Valves are integral to water treatment processes, including filtration, disinfection, and distribution. They control the flow of water, regulate pressure, and facilitate the diversion of water to different treatment stages. Valves enable efficient water management, ensuring the delivery of clean and safe water to consumers.
Power Generation: Power plants rely on valves for controlling the flow of steam, water, or gases in various stages of power generation. Valves are used in boilers, turbines, condensers, and other components to optimize performance, regulate steam or coolant flow, and ensure safety during operation.
Manufacturing and Industrial Processes: Valves are critical in manufacturing industries, where precise control of fluids or gases is essential for production processes. They regulate flow rates, control pressure, and enable the isolation of equipment for maintenance or repairs. Valves facilitate efficient and reliable operation, ensuring product quality and process efficiency.
The importance of valves in these industries cannot be overstated. They provide essential control over fluid or gas flow, enabling efficient operation, system optimization, and safety.
4. Different Types of Valves
Valves come in various types, each designed to serve specific purposes based on the desired flow characteristics and system requirements. Understanding the different valve types is essential for selecting the most suitable valve for a given application. Here are some common types of valves:
Gate Valves: Gate valves are widely used for on-off service in applications that require full flow or complete shut-off. They feature a sliding gate or wedge-shaped disc that moves perpendicular to the flow direction. Gate valves provide a tight seal when fully closed, minimizing pressure drop.
Ball Valves: Ball valves offer reliable and quick control of flow with minimal pressure drop. They consist of a rotating ball with a bore that allows or blocks the flow by aligning or misaligning the bore with the pipeline. Ball valves are commonly used in applications that require rapid opening or closing, as well as precise control.
Globe Valves: Globe valves are versatile valves that are suitable for regulating flow rates. They feature a disc or plug that moves perpendicular to the flow direction, allowing fine control over the flow by adjusting the opening between the disc and seat. Globe valves provide good throttling characteristics and are commonly used in industries where precise control is required.
Check Valves: Check valves, also known as non-return valves or one-way valves, allow fluid or gas to flow in one direction while preventing backflow. They feature a disc or flap that opens under forward flow pressure and closes to prevent reverse flow. Check valves are commonly used in applications where backflow prevention is critical.
Control Valves: Control valves are specifically designed to regulate the flow rate, pressure, or temperature within a system. They consist of a valve body, actuator, and positioner. Control valves provide precise control by modulating the flow in response to signals from a controller or process conditions.
Each type of valve offers distinct advantages, limitations, and typical applications. The selection of the appropriate valve depends on factors such as flow requirements, pressure rating, temperature, material compatibility, and system conditions.
5. Valve Selection and Factors to Consider
When selecting a valve for a specific application, several factors need to be considered to ensure optimal performance and functionality. Here are some key factors to keep in mind:
Flow Requirements: Determine the required flow rate for the application. Consider factors such as the volume of fluid or gas to be transported and the desired flow velocity. This information will help in selecting a valve with an appropriate flow capacity to meet the system's needs.
Pressure Rating: Evaluate the maximum and minimum pressure levels within the system. Choose a valve that can withstand the anticipated pressure conditions without leakage or damage. It's crucial to select a valve with a pressure rating that exceeds the maximum operating pressure to ensure safe and reliable operation.
Temperature Range: Consider the temperature range of the fluid or gas being handled. Different materials have varying temperature limits, and selecting a valve with suitable materials ensures that it can withstand the temperature extremes without degradation or failure. Pay attention to factors such as thermal expansion, contraction, and the impact of high or low temperatures on valve performance.
Material Compatibility: Evaluate the compatibility of the valve materials with the fluid or gas being transported. Certain fluids or gases may be corrosive or reactive, requiring valves made from specific materials to resist degradation. Consider factors such as chemical composition, pH levels, and potential interactions between the fluid or gas and valve materials to ensure long-term durability.
Valve Type: Based on the specific application requirements, select the appropriate valve type. Gate valves are suitable for full flow or shut-off applications, ball valves offer quick and reliable control, globe valves allow for precise flow regulation, check valves prevent backflow, and control valves enable dynamic control based on system conditions. Understand the characteristics and limitations of each valve type to choose the most suitable option.
Operational Environment: Consider the environmental conditions in which the valve will be installed. Factors such as humidity, exposure to UV radiation, presence of corrosive elements, or extreme weather conditions can impact the valve's performance and lifespan. Select a valve that is designed to withstand the specific environmental conditions to ensure reliable operation.
Maintenance and Accessibility: Evaluate the ease of maintenance and accessibility of the valve. Some valves may require periodic maintenance, such as lubrication or replacement of parts, for optimal performance. Consider factors such as ease of disassembly, availability of spare parts, and the need for specialized tools or expertise when selecting a valve.
Compliance and Certifications: Depending on the industry or application, certain valves may need to meet specific standards or certifications. Consider regulatory requirements, industry standards, and certifications such as ISO, API, ANSI, or specific safety certifications when selecting a valve. Ensuring compliance with applicable standards is crucial for safety, reliability, and legal compliance.
By carefully considering these factors during the valve selection process, you can choose a valve that is well-suited to the application's requirements, ensuring efficient and reliable flow control while maximizing system performance and longevity. It is advisable to consult with industry experts or valve manufacturers for guidance and assistance in selecting the most appropriate valve for your specific application.
6. Valve Installation and Maintenance
Proper valve installation and maintenance are crucial for ensuring optimal performance, longevity, and safe operation. Following the recommended practices and guidelines will help prevent issues and maximize the efficiency of the valve system. Here are some instructions for valve installation and maintenance:
Valve Installation:
Pre-Installation Inspection: Before installing a valve, carefully inspect it for any visible damage or defects. Check the valve body, components, seals, and connections for any signs of wear, cracks, or leaks. Ensure that the valve is compatible with the system's requirements, including pressure rating, temperature range, and fluid compatibility.
Proper Alignment: Align the valve correctly with the pipeline or system. Improper alignment can lead to leaks, excessive stress on the valve body, and compromised performance. Use appropriate alignment tools and techniques to ensure proper alignment.
Sealing: Ensure a proper seal by using appropriate gaskets, seals, or packing materials. Follow the manufacturer's instructions to select the correct seal materials based on the fluid or gas being handled. Apply sealants or lubricants as recommended to prevent leaks and ensure a reliable seal.
Tightening Connections: Use the recommended torque values and tightening sequence when connecting the valve to the pipeline or system. Avoid over-tightening, as it can damage the valve or cause leaks. Under-tightening can result in loose connections and potential leakage.
Testing: After installation, perform a thorough leak test to ensure the valve is properly sealed. Apply appropriate test methods, such as pressure testing or visual inspection, to identify and address any leaks or irregularities. Verify that the valve operates smoothly and functions as intended.
Valve Maintenance:
Routine Inspection: Regularly inspect valves for signs of wear, corrosion, or damage. Check for leaks, loose connections, or unusual operating conditions. Address any issues promptly to prevent further damage or performance degradation.
Lubrication: Follow the manufacturer's guidelines for lubricating the valve components. Proper lubrication reduces friction, enhances operation, and prolongs the lifespan of the valve. Use the recommended lubricants suitable for the valve type and application.
Cleaning: Clean the valve and its components periodically to remove debris, sediment, or contaminants that can affect performance. Use suitable cleaning agents or solvents as recommended by the manufacturer. Ensure proper disposal of cleaning materials and adhere to environmental regulations.
Stem and Actuator Maintenance: Pay attention to the stem and actuator components of the valve. Inspect for proper alignment, smooth operation, and signs of wear. Lubricate or replace stem seals, gaskets, or packing materials as necessary.
Calibration and Adjustment: Periodically calibrate and adjust control valves or valves with specific settings to ensure accurate operation. Follow the manufacturer's guidelines or consult with experts to perform the calibration and adjustment procedures correctly.
Record Keeping: Maintain a detailed record of valve installation, maintenance activities, and inspections. Keep track of maintenance schedules, repairs, and any changes made to the valve system. This information will help in tracking the valve's history and aid future maintenance or troubleshooting efforts.
Training and Expertise: Ensure that personnel responsible for valve maintenance and operation receive proper training and have the necessary expertise. Understanding the specific valve type, its components, and maintenance requirements is essential for effective valve management.
By following these installation and maintenance practices, you can ensure that valves operate efficiently, minimize the risk of leaks or failures, and extend their operational lifespan. Regular maintenance and proactive inspection help identify potential issues early, allowing for timely repairs and optimization of valve performance.
7. Innovations and Emerging Trends in Valve Technology
The field of valve technology has witnessed significant advancements in recent years, driven by the need for improved performance, efficiency, and automation. These innovations have introduced new features, materials, and designs that enhance valve functionality and address industry challenges. Here is an overview of recent innovations and emerging trends in valve technology:
Smart Valves: Smart valves incorporate advanced technology, such as sensors, actuators, and communication capabilities, to enable real-time monitoring, control, and data analysis. These valves can provide valuable information on factors like flow rates, pressure, temperature, and valve health, allowing for remote monitoring, predictive maintenance, and process optimization. Smart valves improve operational efficiency, reduce downtime, and enhance overall system performance.
Remote Monitoring and Control: The integration of wireless communication and Industrial Internet of Things (IIoT) technologies has enabled remote monitoring and control of valves. This allows operators to monitor valve performance, receive alerts on abnormal conditions, and make adjustments remotely. Remote monitoring improves efficiency, reduces manual interventions, and enables timely response to valve-related issues.
Automation and Actuation: Automation technologies, such as motorized actuators and pneumatic actuators, have gained prominence in valve control systems. These actuators offer precise and reliable control, enabling rapid response to process changes and facilitating integration with automated control systems. Automation improves system efficiency, accuracy, and repeatability while reducing the reliance on manual operation.
Enhanced Valve Materials: Advances in materials science have introduced new materials and coatings that enhance valve durability, resistance to wear, corrosion, and erosion. High-performance materials like stainless steel, alloys, and ceramics are being used to extend the lifespan of valves, especially in harsh environments or corrosive applications. These materials improve reliability, reduce maintenance needs, and enhance overall valve performance.
Improved Sealing Technology: Sealing is a critical aspect of valve performance, and advancements in sealing technology have led to enhanced leak-tightness and reduced fugitive emissions. Innovative sealing materials, such as elastomers and advanced polymers, provide excellent sealing properties and resilience, even in challenging conditions. Additionally, improved seal designs and manufacturing techniques contribute to longer service life and improved environmental sustainability.
Energy Efficiency: Energy consumption is a significant consideration in valve systems. Efforts are being made to design valves with reduced pressure drops, efficient flow characteristics, and optimized actuation systems. By minimizing energy losses and optimizing flow control, these energy-efficient valves contribute to lower operational costs, reduced environmental impact, and improved sustainability.
Integration with Digital Control Systems: Valves are increasingly being integrated into digital control systems, such as Distributed Control Systems (DCS) and Programmable Logic Controllers (PLC). This integration allows for seamless communication, integration, and coordination with other components and systems. Digital control systems enable precise and coordinated valve control, data acquisition, and advanced process optimization.
Enhanced Safety Features: Safety is a paramount concern in valve applications, and innovations in valve technology have introduced enhanced safety features. These include pressure relief valves, emergency shut-off mechanisms, and fail-safe systems that ensure proper valve operation, prevent overpressure situations, and mitigate potential hazards.
Sustainable Valve Design: Valve manufacturers are increasingly focusing on sustainability, incorporating eco-friendly design principles and manufacturing processes. This includes the use of recyclable materials, reducing energy consumption during production, and optimizing valve designs for minimal environmental impact.
These innovations and emerging trends in valve technology are driving improvements in performance, efficiency, safety, and sustainability. The adoption of smart valves, remote monitoring, automation, and advanced materials is transforming the valve industry and paving the way for more intelligent, efficient, and reliable valve systems.
8. Safety Considerations in Valve Operations
Safety is of paramount importance when working with valves, as improper operation or failure can lead to accidents, equipment damage, or environmental hazards. Following safety protocols and guidelines is crucial to ensure the well-being of personnel, protect assets, and maintain regulatory compliance. Here are important considerations for safe valve operations:
Follow Safety Guidelines: Familiarize yourself with and adhere to industry-specific safety guidelines, regulatory requirements, and company policies. These guidelines provide essential information on safe practices, personal protective equipment (PPE), and emergency procedures.
Proper Training: Ensure that personnel involved in valve operations receive proper training on valve handling, operation, and maintenance. Training should cover topics such as valve types, identification, proper operation, and response to emergency situations. Well-trained personnel are better equipped to operate valves safely and respond effectively in case of emergencies.
Equipment Inspection: Regularly inspect valves, associated equipment, and safety devices for proper functioning. Check for leaks, signs of wear, corrosion, or mechanical damage. Ensure that safety features such as pressure relief valves, emergency shut-off systems, or limit switches are in good working condition.
Pressure Relief: Use appropriate pressure relief valves or devices to prevent overpressure situations. Ensure that pressure relief devices are properly sized, set, and tested to provide reliable protection against excessive pressure buildup. Regularly inspect and maintain these devices to ensure their effectiveness.
Lockout/Tagout Procedures: Implement and strictly follow lockout/tagout procedures when working on valves. This ensures that valves are isolated from energy sources, preventing accidental startup or release of stored energy. Lockout/tagout procedures protect personnel from injury during maintenance or repair activities.
System Isolation: Before performing maintenance or repair tasks on valves, properly isolate the system and release any trapped pressure or fluids. Follow proper procedures for system depressurization, draining, or flushing to eliminate potential hazards and ensure a safe working environment.
Ventilation: Ensure adequate ventilation when working in confined spaces or areas with potentially hazardous gases or vapors. Proper ventilation helps prevent the buildup of flammable or toxic gases and maintains a safe working atmosphere.
Personal Protective Equipment (PPE): Wear appropriate PPE when working with valves, especially in hazardous environments. PPE may include safety glasses, gloves, protective clothing, hearing protection, or respiratory protection, depending on the specific hazards involved. Adhere to the manufacturer's instructions and company policies regarding the use of PPE.
Emergency Preparedness: Be prepared for emergencies by having a well-defined emergency response plan. Identify potential risks, establish communication protocols, and provide training on emergency procedures. Ensure that emergency shutdown systems, alarms, and emergency equipment are regularly tested and maintained.
Proper Documentation: Maintain accurate records of valve operations, maintenance activities, inspections, and safety procedures. Document any incidents, near misses, or deviations from standard procedures. This information can be valuable for future reference, analysis, and continuous improvement of safety practices.
By prioritizing safety considerations in valve operations, you can mitigate risks, prevent accidents, and ensure the well-being of personnel and equipment. Regular training, adherence to safety guidelines, and a proactive approach to maintenance and inspections contribute to a safe working environment and reliable valve performance.
9. Frequently Asked Questions about Valves
What is the purpose of a valve?
A valve controls the flow of fluids or gases within a system. It can start, stop, or regulate the flow, allowing for efficient operation and control over the medium being transported.
How do valves control the flow of fluids or gases?
Valves control the flow by opening, closing, or partially obstructing the passage within a system. They can be manually operated or automated, using various mechanisms such as gates, balls, discs, or plugs to regulate the flow.
What are the different types of valves?
There are several types of valves, including gate valves, ball valves, globe valves, check valves, and control valves. Each type has its specific design, features, and applications, enabling different levels of flow control and functionality.
How do gate valves work?
Gate valves have a sliding gate or wedge-shaped disc that moves perpendicular to the flow direction. When fully open, the gate allows unobstructed flow, and when closed, it creates a tight seal to stop the flow completely.
What are ball valves used for?
Ball valves use a rotating ball with a bore to control the flow. They offer quick and reliable control, allowing for rapid opening, closing, or adjustment of the flow. Ball valves are commonly used in applications where tight shut-off and precise control are required.
What are globe valves used for?
Globe valves are suitable for regulating flow rates. They feature a disc or plug that moves perpendicular to the flow direction, allowing for fine control by adjusting the opening between the disc and seat. Globe valves provide good throttling characteristics and are commonly used in applications that require precise flow control.
What is the advantage of using check valves?
Check valves, also known as non-return valves or one-way valves, allow fluid or gas to flow in one direction while preventing backflow. They automatically close when the flow reverses, preventing any backward movement. Check valves are crucial for preventing backflow and protecting equipment in systems where backflow could cause damage.
How do control valves work?
Control valves regulate the flow, pressure, or temperature within a system based on signals from a controller or process conditions. They consist of a valve body, actuator, and positioner, which work together to modulate the flow and maintain the desired process parameters.
What factors should be considered when selecting a valve?
When selecting a valve, factors such as flow requirements, pressure rating, temperature range, material compatibility, and environmental conditions should be considered. These factors ensure that the valve is suitable for the specific application and can operate safely and efficiently.
How often should valves be maintained?
Valves should be regularly inspected and maintained to ensure optimal performance. The frequency of maintenance depends on factors such as the type of valve, the application, and the operating conditions. It is recommended to follow the manufacturer's guidelines and industry best practices for maintenance intervals and procedures.
These frequently asked questions provide a basic understanding of valves, their functions, and their applications. For more specific information related to valve sizing, leakage prevention, or maintenance practices, consult valve manufacturers, industry experts, or refer to relevant industry standards and guidelines.